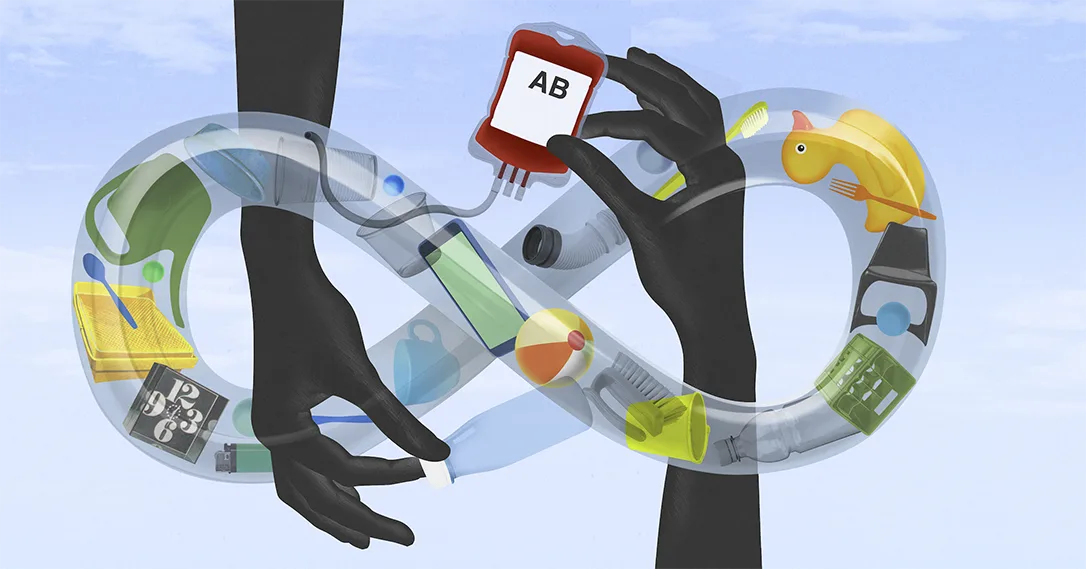
Circular economy
18 minute read
Where next for plastic?
Words: Lucy Siegle. Illustration: Brett Ryder
The environmental impact of plastic is a problem in search of urgent solutions. But as pathways to better production, usage and reclamation emerge, how do we make them count? And what does the future look like if we succeed? Environmental writer Lucy Siegle examines some of the ideas, technologies and opportunities on the frontlines of the plastic revolution.
Expect to learn:
What the experts say about our society’s changing relationship with plastic
What the emerging technologies and innovations in plastic recycling are – and how an important gap in this system could be closed
What the role of a ‘systemic shift’ is in the roadmap to a more sustainable future with plastic
The contours of catastrophe are never easy to define. As we’re finding out in this time of COVID-19, it is not always straightforward to find the ‘emergency exit’ sign in the midst of a crisis. The issue of global plastic waste, specifically the estimated 8–12 million tonnes that continues to leak into the world’s oceans each year, has been referred to as “the plastic pandemic”.
Now that we are in the middle of a real pandemic, we may hear that language toned down, but what we cannot dial down is our concern over the very real threat plastic waste poses to our ecosystems. The fallout from coronavirus will likely shape global economies, political spheres and social structures for decades to come, but plastic pollution is no less of a generation-defining crisis – and its possible solutions sometimes seem just as difficult for us to grasp.
The decade between 2002 to 2012 saw more plastic produced than any other time on Earth
Right now, there are two existential challenges facing the plastic industry. The first is the demand of increasing volume as conventional, virgin fossil oil-based production is predicted to rise. Then there is the legacy issue: since the 1950s an amount of plastic equivalent to the weight of one billion elephants has been produced, and 79% of that is still with us. The decade between 2002 to 2012 saw more plastic produced than at any other time on Earth, and a worrying amount of that already seems to be ending up in the sea. As the Ellen MacArthur Foundation puts it, without radical action by 2050 there could be more plastic in the ocean than fish.
Not every crisis has a water-cooler moment, but this one did. And it came in a way that nobody – even the people behind it – could have foreseen. With the inclusion of one short sequence on plastic waste and its impact on wildlife at the end of the BBC natural history series Blue Planet II, hundreds of millions of viewers worldwide saw and listened to something they didn’t necessarily want to hear.
What started as an epiphany quickly gained international traction. Its waves spread, from corporations dropping single-use plastics, to taxes levied on disposable shopping bags and even a Plastic Pact between UN signatories at the global environment summit in Kenya in 2018.
But was it enough? As many have observed, there is still no equivalent to the global Montreal Protocols that helped to solve the ozone crisis. In addition, the plastic industry has felt demonised and has often reacted defensively. At the same time, a galvanized public has often not fully understood how deeply embedded plastic is in the supply chains it still relies on.
An opportunity to re-engineer the whole system and reassess our relationship with plastic is appearing
Three years on from The Blue Planet II, pressure has continued to build from many stakeholders – including civil society, environmental NGOs, governments, scientists, innovation labs, marine conservationists and many others. But at the same time, a unique opportunity to re-engineer the whole system and reassess our relationship with plastic is appearing.
Alongside major learnings, some breakthroughs and incremental progress in all phases from production and manufacture to usage and disposal, the last few years have seen genuine progress. As the world shifts its attention to a more imminent crisis, many technical and social solutions to the plastic problem are about to come of age.
As we prepare to move into a new solutions-oriented mindset, what examples of progress will continue to form a major part of that pathway? And when, finally, we will be able to turn the tide on plastic waste
Seeing the bigger picture
In the wave of sentiment that followed Blue Planet II, we saw a uniquely powerful force in action. In the age of social media and online activism, the way that civil society tends to flex its muscles is increasingly felt through petitions singling out particularly problematic offenders. For example, in the EU, citizens have come together to push legislators for bans on plastic straws and coffee stirrers. Crowd-driven campaigns have helped to push change, but they also contain built in limitations.
One weakness of relying on public pressure to force change is the acceptance that people easily get distracted, causing society to reprioritize. Who, for example, was still petitioning supermarkets to remove unnecessary plastic wrap during the outbreak of COVID-19? Another limitation of the item-by-item approach is that once you’ve dealt with one source of pollution, another will inevitably take its place. Picking our battles one at a time, we find ourselves in a never-ending cycle of chasing down plastic pollutants, instead of working towards a complete and total system shift.
Elsewhere, public-driven campaigns that rely on legislation can fall short of the change promised. When the UK’s ban on microbeads in cosmetics was introduced in 2018 it was described by the government as “world leading” and seemed a very necessary response to prevent adding to the estimated 51 trillion microplastic particles that are currently held in the world’s oceans. But a recent report by environmental think tank and policy specialists Green Alliance points out that the ban in effect ignored 90% of the added microplastics that still pollute the environment from other sources.
Any time you are using solutions that are not based on drilling for fossil fuels, you have the opportunity to dramatically reduce your CO2 burden
But shift the lens to industry, away from civil society’s response and legislative loopholes, and there are some major opportunities to address other segments of the plastic waste problem. While the focus has understandably centred on the impact of leakage from the plastic production system on the natural environment, the carbon intensity of plastic represents a critical issue that needs to be urgently addressed. When it comes to affecting substantial change in the arena of plastic manufacturing, decoupling the material from virgin fossil oil feedstock is an area where genuine change can take place.
“A lot of the problem with CO2 is not only from cars and aviation, but from the other industries using fossil oil”, explains Mercedes Alonso, Executive Vice President for Renewable Polymers and Chemicals at Neste, the company working towards replacing fossil oil in road transport, aviation, and the plastic industry with renewable solutions.
“The fossil fuel burden is particularly high any time you are involved in drilling [crude oil]. The flipside of that is that any time you are using solutions that are not based on drilling for fossil oil, you have the opportunity to dramatically reduce your CO2 burden” explains Alonso.
Indeed, researchers at Stanford University published a study on the carbon intensity of oil production in 2018 and found that production emitted between 10.3 grams to 15 grams of emissions for every megajoule of crude oil that was drilled.
The stage is then set for bio-based plastics (or bioplastics), which have taken a while to find their groove.
Seeking more sustainable solutions
Over the last 10 years the bio-based plastics industry has been able to overcome a number of challenges. Early incarnations made from maize and sugar cane seemed to be in direct competition with the food value chain. Over the last decade researchers have concentrated on working towards bio-based plastics by creating different monomers alongside the food industry. So instead of competing for land used for plants grown for food production, the by-products of crop processing can now be used to make bioplastics instead. The applications for such bio-based polymers are endless, leading to an achievable future where practically any polymer could, potentially, be made from renewable material.
Neste is the world's largest producer of renewable diesel, and they have been working with partners to produce bio-based polymers from waste and residues at commercial scale. Already these renewable plastics, notably polypropylene and polyethylene, are being commercialized and are suitable for car parts, consumer electronics and packaging, to name a few.
It’s still early days for us to analyse the data on the bio-based plastic products that have arrived on the marketplace so far. Still, a 2019 study from researchers at the University of Utrecht on ‘Environmental impact assessments of innovative bio-based products’, one of the very first environmental LCA (or life cycle assessment) studies, verified that when conventional petrochemical PP-plastic in a plastic cup is replaced with bio-based PP-plastic – produced with Neste’s renewable hydrocarbons from used cooking oil – climate change impact was reduced by 40–62% and fossil fuel resource use by an astonishing 80–86%. By any measure, that is a major win.
How do we ensure that this shift in manufacturing continues in the long-term?
When we scan the possible solutions to any environmental crisis, it is obviously important that we do it in a real-world context. The solutions that have the most potential are the ones that are already embedded in the production cycle, so they minimize or even eliminate the need for changes – and can offer a viable drop-in response from the decision makers at every step of the process. Neste’s NEXBTL technology is a solution that fits this criteria. It allows the production of drop-in feedstock for bio-based plastics to be manufactured via the chemical industry’s conventional steam crackers and processed into plastic parts without any changes in equipment by converters/molders. The resulting are recyclable just like virgin fossil fuel based plastics.
“Our experts understand crackers so they can work with producing partners to advocate for our material versus crude oil,” Alonso explains, “This is about working through any concerns and logistics, as well as understanding the economic value. How can we create other bio-based polymers that are not only polyethylene or polypropylene? We need to ensure that this shift in manufacturing, this investment, continues to work in the long-term.”
The legacy issue
Years before Blue Planet II, another TV event galvanised public opinion behind an environmental crisis. In 1987, a so-called ‘garbage barge’ containing household trash from New York City was filmed floating along the East Coast of America. The barge was owned by Lowell Harrelson, a waste entrepreneur who planned to dump the trash in Central America after finding New Jersey’s main landfill site too expensive. Understandably, the authorities in Central America weren’t too keen on the idea. Slowly, the barge rumbled its way back to New York, closely followed by the TV cameras, and Mr Harrelson finally coughed up for the landfill fees.
Since then, offloading waste to low wage economies has become commonplace but remains controversial. One of the most significant interventions to stop the dumping of plastic waste on developing and emerging economies has come via the United Nations. In May 2019 under the terms of the Basel Convention on Hazardous substances, low-grade plastic waste was reclassified, and countries were given the power to refuse to accept it. It is thought that this treaty will particularly affect the US, which in 2018 alone exported 157,000 large shipping containers of mixed plastic wastes to developing countries.
It’s not easy to put a stop to the dumping of plastic waste. A pragmatic solution therefore is for organisations to build coalitions, including brands dependent on plastic for their products, to invest in waste solutions and provide infrastructure.
We might ask ourselves what we are doing wrong. More importantly though, we have to also ask what we might already be doing right
One of the best known is Project STOP, launched in 2017 by Borealis and SYSTEMIQ, that designs, implements, and scales circular economy solutions to prevent plastic pollution in Southeast Asia. One such test case is Jembrana, Bali where 80 people now work full time on waste collection for an area serving 47,500 people. But what about the problems that exist in our own backyard?
For those of us in nations that remain recalcitrant about recycling, and where figures on plastic recycling have plateaued, we might ask ourselves what we are doing wrong. More importantly though, we have to also ask what we might already be doing right – with some industries offering potential solutions through long-term investment in technologies designed to wring the most out of our existing plastics and providing complementary solutions to the current mechanical recycling systems that are in place.
“Recycling is complicated,” admits Alonso. “You can’t just make waste a valuable product overnight without buy-in from everybody. There is a whole complex chain of collecting, sorting and widening the plastic streams that are in place.”
Plugging the gap
Modern mechanical recycling of plastic continues to be a story of incremental innovation, if not overnight success. There has been progress, particularly around the correct identification and sorting of materials in order to assure good quality recyclate. Recycling plants and Mixed Recovery Facilities have invested in technologies such as near infrared spectroscopy (NIR), laser or x-ray techniques to make identification more precise. There has also been investment in tackling some stubborn consumer goods, such as black food trays.
Recycled plastics derived from mechanical processes are widespread in the automotive and construction industry, and there are new opportunities opening up every day too: while road aggregate from plastic waste is more common in India, it also has a recent history of being used in similar projects in Europe. The more markets that evolve and adapt themselves for recycled material, the more places it can go.
This is plastic recycling at its highest level – there are no limitations to its application
Yet, once again, this isn’t the whole story. Recycled plastic lends itself well enough to applications such as road aggregate, but turning food and medical-grade packaging right back into things like juice bottles and surgical gloves is challenging if not impossible in mechanical systems. We might call this the Recycling Gap.
Researchers, including those at Neste, have recently seen an opportunity to close that gap, looking at the large chunk of plastic that cannot be easily recycled. Working with a technology called chemical recycling, scientists have harnessed the potential of a thermochemical process that effectively breaks polymer molecules down, giving them the ability to turn it into a material similar to crude oil.
This process has the advantage of being able to turn normally hard-to-recycle plastic such as films, bags and laminated plastics, into an oil via thermal cracking or pyrolysis.
It’s exciting stuff, and Alonso shows it when she goes into more detail. “This form of recycling can be considered recycling at its highest level,” she explains. “Any polymer that you make out of this will be exactly the same as a fossil oil-based one. There are no limitations to their applications. They can even be used for food or in a medical context.”
Once capacity is built for chemical recycling, the numbers can quickly climb. In October 2019, REMONDIS and Neste partnered up to develop chemical recycling of plastic waste, and a month later, Neste and Ravago announced a similar collaboration. Together, these collaborations aim at developing capacity to chemically recycle 400,000 tonnes of plastic waste every year. Another project will see a plant in the UK chemically recycle 7,000 tonnes of plastic a year, turning waste into Plaxx oil, a recycled hydrocarbon feedstock for the manufacturing of new, virgin-quality plastics.
Looking to nature
But what about potential solutions that already exist? Not a day goes by without a headline grabbing story about something in nature that will solve the plastic crisis. A recent example saw a caterpillar that appeared to be happy to exist on a diet of old plastic bags. There is, however, always a catch (in this case the caterpillar ate the bags so slowly that it would never be able to make an impact).
But a surprise discovery in 2018 by an international team of scientists studying a plastic-eating enzyme has proved to be rather more promising. In this case, the researchers accidentally engineered an enzyme first discovered at a Japanese recycling centre to work fast and efficiently enough to be considered a major breakthrough.
The race is now on to scour the globe in search of more enzymes that will devour plastics
"Enzymes work like a lock and key”, explains professor John McGeehan from the University of Portsmouth in the UK, who helped lead the international team. “They recognise the shape and structure of the polymer.” The enzyme turbo-charged by McGeehan’s team is spectacularly good at devouring the binds of the polymer in PET plastic (one of the most widely used plastics, commonly found in single use drinks bottles) leaving the monomers free.
This enzyme, known as PETease, is being trialled in a recycling centre in the UK, but other enzymes will be needed to ‘unlock’ other plastics. “If you look at the grid of 10 common types of plastic, we’re on number one”, said McGeehan. The race is now on as his colleagues continue to scour the globe in search of more enzymes that will devour other plastics.
Built-in obsolescence
As industry continues to seek new answers to even newer problems, there is clearly no one quick fix to fit the whole plastic crisis (and we should probably be wary of anyone that claims to have found it). But while most researchers look for ways to adapt production cycles and deal with existing waste deposits, one company already is working on a backup plan.
Polymateria, based in the Imperial college innovation labs in West London, has developed a biotransformation technology that aims to solve the plastic problem before it occurs. Niall Dunne, the CEO of Polymateria, describes his technology as ‘a probiotic’ for plastics, dropped in during masterbatch production to enable total biodegradability should it be needed.
If we accept that some plastics are embedded into modern supply chains, then it’s a good idea to focus on a solution for the percentage that slips the net
Polymateria’s biotransformative technology alters the plastic at a molecular level. When a plastic pot is on the supermarket shelf or sitting in your cupboard, the technology lies dormant. The empty pot can and should be recycled in the standard system. But if the pot ever ends up falling off a barge, rolling down a hill and landing in a river, biodegradation is triggered. The technology essentially opens up the polymer chain so that the natural agents of decay – ultraviolet light, moisture and air – can set to work. Meanwhile the plastic contains probiotics that draw in microbes, setting another natural agent of decay to work.
If this pays off, consumers could soon be handling products – from hot drinks to chip bags and fruit netting – that promise total biodegradability. The technology is ready according to Dunne, and the focus now is on making sure that the consumer understands it. Early modelling shows that this solution particularly chimes with younger consumers who have grown up with ‘use by dates’. Why not have a packet that also has a ‘recycle by’ date, after which it will begin to break down? There is a pragmatism about this intervention. It accepts that plastics are embedded into modern supply chains and therefore we must focus on a solution for the percentage that slips the net and ends up as pollution in our oceans.
Which future do we choose?
In the coming months The Pew Charitable Trust is expected to publish the results of a two-year process with global consulting firm SYSTEMIQ where solutions to the global plastic crisis have been extensively mapped. These results will act as an important resource for industry looking to assess the best areas to direct their efforts and attention. They will help gauge the most effective strategies to tackle plastic’s environmental footprint and will help us all judge the gap between where we are now, and where we need to be.
Given the projected rise in the production of oil-based plastics, there isn’t a moment to waste. Despite the best efforts of researchers, campaigners and industries around the world, it can seem daunting.
Every solution has its place, but the important thing is that they all add up to a decisive shift
But Neste’s Mercedes Alonso is cautiously optimistic about the future. “We have reached the point where we are really looking at things from a much broader point of view because climate change has really brought us to the point,” she says.
“Sometimes it’s about big system shifts,” says Alonso. “Sometimes it’s about informing the consumer that there’s a better way of keeping their food fresh. We will see more and more solutions. Every solution has its place, but the important thing is that they all add up to a decisive shift, together.”
“There is push and pull on all of this. We don’t have much time to achieve progress; but luckily there is a renewed sense of urgency inside the industry.”
So in this game of possible worlds, which future will we choose? Will we seize the chances we’ve been given to limit the impact of plastic? Or let them pass, and fail to stop the tide?
The answer is in all of our hands: governments, industry, researchers, technologists, campaigners, media – and, ultimately, yours and mine.
Neste's solution for plastics
Neste has developed a drop-in solution from renewable and recycled raw materials that can be used on its own or in a blend to create plastic products of identical quality to those made out of conventional raw materials based on virgin fossil oil.