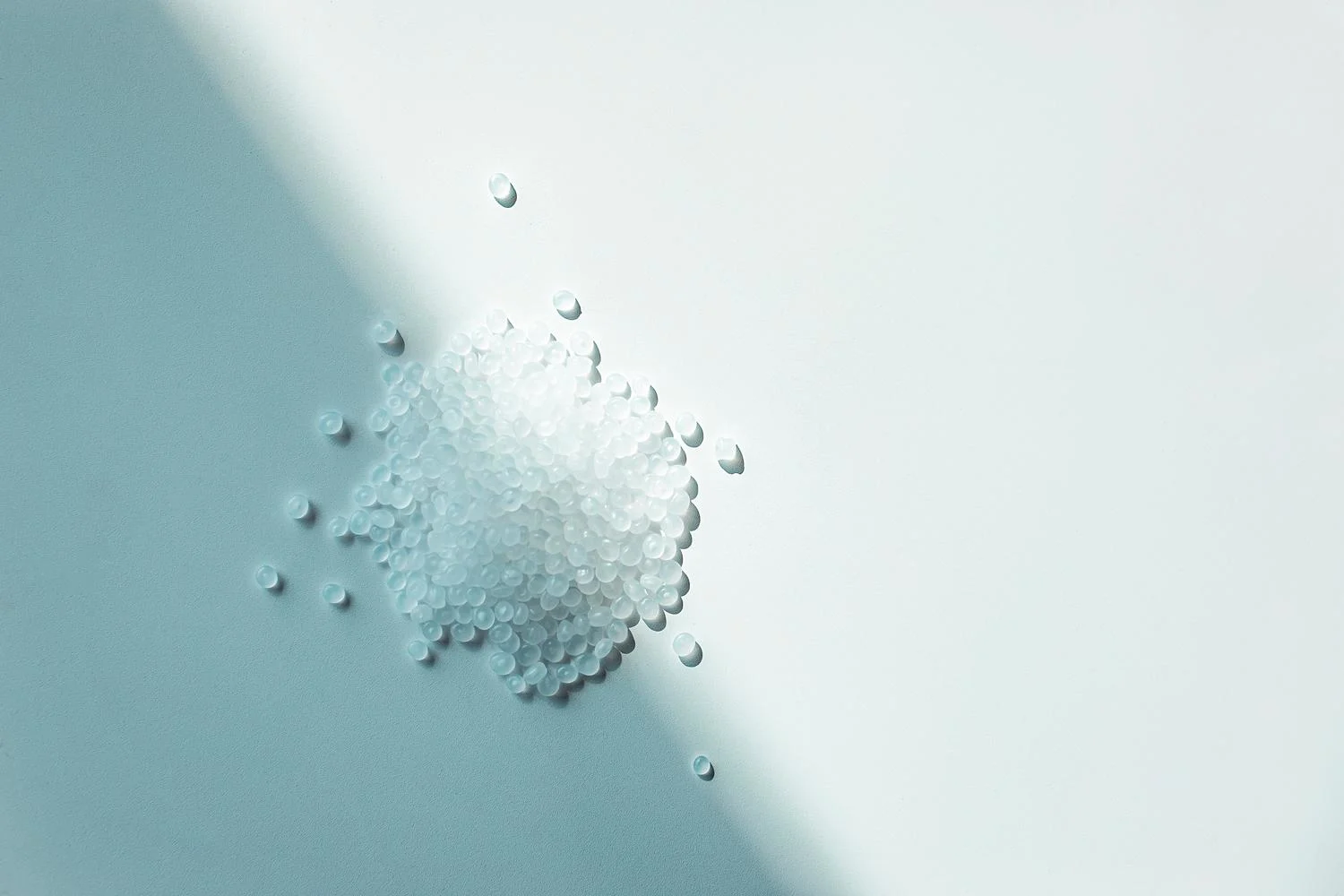
Plastics
8 minute read
3 Things you need to know about chemically recycled plastic
We spoke with Heikki Färkkilä, Vice President of Chemical Recycling at Neste, to dive deeper into the world of chemical recycling and to understand what exciting breakthroughs are on the horizon for the fast-moving industry.
How will we recycle plastics twenty years in the future? According to Heikki Färkkilä, Vice President of Chemical Recycling at Neste, “The big breakthrough and the vision of the industry should be to create the ability to run the whole system based on recycled and renewable feedstock, without any virgin fossil feeds.”
Färkkilä is particularly focused on the role of recycling in this picture. He envisions a future where communities around the world process their own waste locally, and turn plastics that would otherwise become landfill or end up in incineration, into new materials, which can then be traded internationally. Waste would become a valuable commodity in this scenario, but instead of thinking on a local-scale only, Färkkilä sees that we should move towards circularity in plastics at an international scale. “We should rethink our approach to plastics all the way from product design to collection of materials for reuse and recycling. And chemical recycling will need to play a much bigger role than it does today.”
Färkkilä predicts that there are three bigger breakthroughs that will happen over the next few decades to make this future possible: a global circular infrastructure, risk-free investing in chemical recycling, and multiple changes in regulations.
Breakthrough 1: Creating a risk-free industry for investors
From a scientific point of view, chemical recycling is not a problem. Several chemical recycling technologies have already been proven to work, such as gasification, depolymerisation and thermal liquefaction. But at the moment they’re mostly used at small-scale demonstration sites with the first commercial units just starting their operations. “I believe in the coexistence of several different technologies,” says Färkkilä. “Each one of those have their advantages, and they are differently suited for different types of materials.
”In his vision of the future, where chemical recycling is handled locally at different sites around the world, each location would choose a combination of various recycling technologies best fit for the volume and the type of waste streams at hand. But for that to be possible and affordable, these technologies need to move from demonstration scale to industrial scale, and that’s where Färkkilä thinks we need a breakthrough: “Investing in chemical recycling technologies needs to be less risky, so that they can be considered also by pension funds, waste management, or utility companies that are typically operating in relatively low-risk environments.”
At the moment, it may be difficult for investors to truly assess how mature new recycling technologies and the business models around them really are. To make the progress of the industry more transparent and demonstrate the new solutions scaling up, Färkkilä would like to see companies already using chemical recycling sharing how much waste they’ve turned into feedstock and how much plastic they have produced that way. “I would like to see the entire industry start making these volumes transparent as that is the only way to show progress as technologies develop."
Having clarity about the actual scale of different chemical recycling methods will make it easier for investors to decide which technologies to support, and this will eventually lead to larger scale and more affordable chemical recycling solutions that have the potential to become much more widespread. Färkkilä already sees an existing demand for chemical recycling.
”There's far more demand for recycled resins than there is supply.” This demand is coming especially from industries that currently can’t use mechanically recycled plastics. For example, medical applications, certain food packaging or children’s toys can now only be made with virgin plastics, but plastics made from chemically recycled feedstocks could meet the same quality criteria. However, brand owner and consumer demand cannot alone drive the full-scale global substitution of virgin fossil materials with recycled and renewable ones, which leads us to the next required breakthrough.
Breakthrough 2: Consistent and clear international regulations
“As chemical recycling is still a novel technology, the regulation around it has been very ambiguous,” says Färkkilä, “As an example it has been unclear whether chemical recycling would be considered recycling when accounting for regulatory recycling targets.”
As long as regulations use recycling definitions that only include mechanical recycling, there are limited incentives for chemical recycling. But Färkkilä is pleased to see this starting to change: “First leading countries in Europe are now recognizing that we are not talking about competition between mechanical recycling and chemical recycling but building a portfolio of complementary solutions.” That is reflected in regulations that consider chemical recycling as a form of recycling, and not identical to energy recovery or landfilling.
We are not talking about competition between mechanical recycling and chemical recycling, but really building a portfolio of complementary solutions.
Once it becomes clear which chemical recycling methods are likely to be widely used for the processing of waste plastics, it will also become possible to implement regulations around standardising the quality of the feedstock or the final product. That would include international regulations, to facilitate cross-border trade of feedstocks. At the moment, Färkkilä thinks it’s not yet possible to talk about quality standards because we don’t yet know which methods will turn out to be the dominant chemical recycling technologies, but he adds “I do believe that over time talk about the quality of the material will become more standardized.”
Breakthrough 3: Value of plastic material driving investment into waste collection globally
The biggest change needed would be to expand the infrastructure for collecting and processing waste. At the moment, plastic waste collection is far from perfect.“Plastic does not end up in the oceans because it wasn't recycled,” says Färkkilä, “it ends up in the oceans because it wasn't properly collected and managed. Besides causing major environmental problems, failing to direct it to circulation is a massive failure in resource efficiency.”
We do not yet have proper recycling solutions in place for many types of plastic packaging. Without those solutions, a big part of the plastic waste we produce becomes merely a cost item, not a valuable resource to be reused. Chemical recycling has the potential to change that.
“In the grand scheme of things, transporting plastic waste over long distances doesn't make a lot of sense.” Instead, Färkkilä thinks we should be aiming for local solutions and involving chemical recycling. Still, he adds, “there will always be -- and there should be -- a relevant waste stream that goes to mechanical recycling.” But mechanical recycling doesn’t quite create the same quality plastics as the original virgin plastics, and each piece of plastic can only go through a few rounds of mechanical recycling at most. “That's where chemical recycling comes into play,” Färkkilä explains. Chemical recycling breaks down the plastics to its molecular components which can be used to create a completely new plastic. In the process plastic waste which today is only a cost item is converted into a valuable commodity. It can be traded and exported and returned into the plastics industry around the world. And Färkkilä hopes to see a network of decentralised chemical recycling facilities around the world. These could operate at a regional level, or even a local level for large cities - a step up from the current demonstration scale but not so large that it would require waste to be transported very far.
“The first stage of the recycling solution needs to be relatively small-scale and relatively low-cost,” he says. This would enable different countries or regions to collect their own local plastic waste and convert it with chemical recycling to a feedstock for the plastics industry.
Those waste plastic based feedstocks need to become a traded commodity.
This new infrastructure requires a tight collaboration between waste processing facilities and the plastics industry to get the product quality right. But that alone is not enough. For this to be truly a global effort, Färkkilä says that “we need to be working on the cost curve to get benefits of large numbers and scale, so that developing economies can also afford solutions like this.”
So, these three milestones, each of them consisting of multiple areas that need to be developed, can eventually make it possible to achieve Färkkilä’s vision of a plastic industry that runs almost entirely on recycled and renewable feedstock. While, in the long-term, recycling is the backbone of a plastics industry free of virgin fossil resources, renewable materials also play an important role in the equation. No collection and recycling value chain is free of any losses and these can be compensated for with renewable resources. What is important is that the renewable based materials are compatible with the rest of the plastics value chain.
“It is my vision, not a dream”, Färkkilä says, “I believe it is not a question about ‘if it will happen’ as we simply must combat the global plastic waste challenge and reduce our reliance on virgin fossil resources with the best possible technologies. And, in my opinion, chemical recycling is one of those. The only remaining question, therefore, is how fast can we make this vision a reality?”
Credits: Dr. Eva Amsen, a science writer and communicator whose work has appeared on Forbes, Nautilus and The Scientist. Twitter