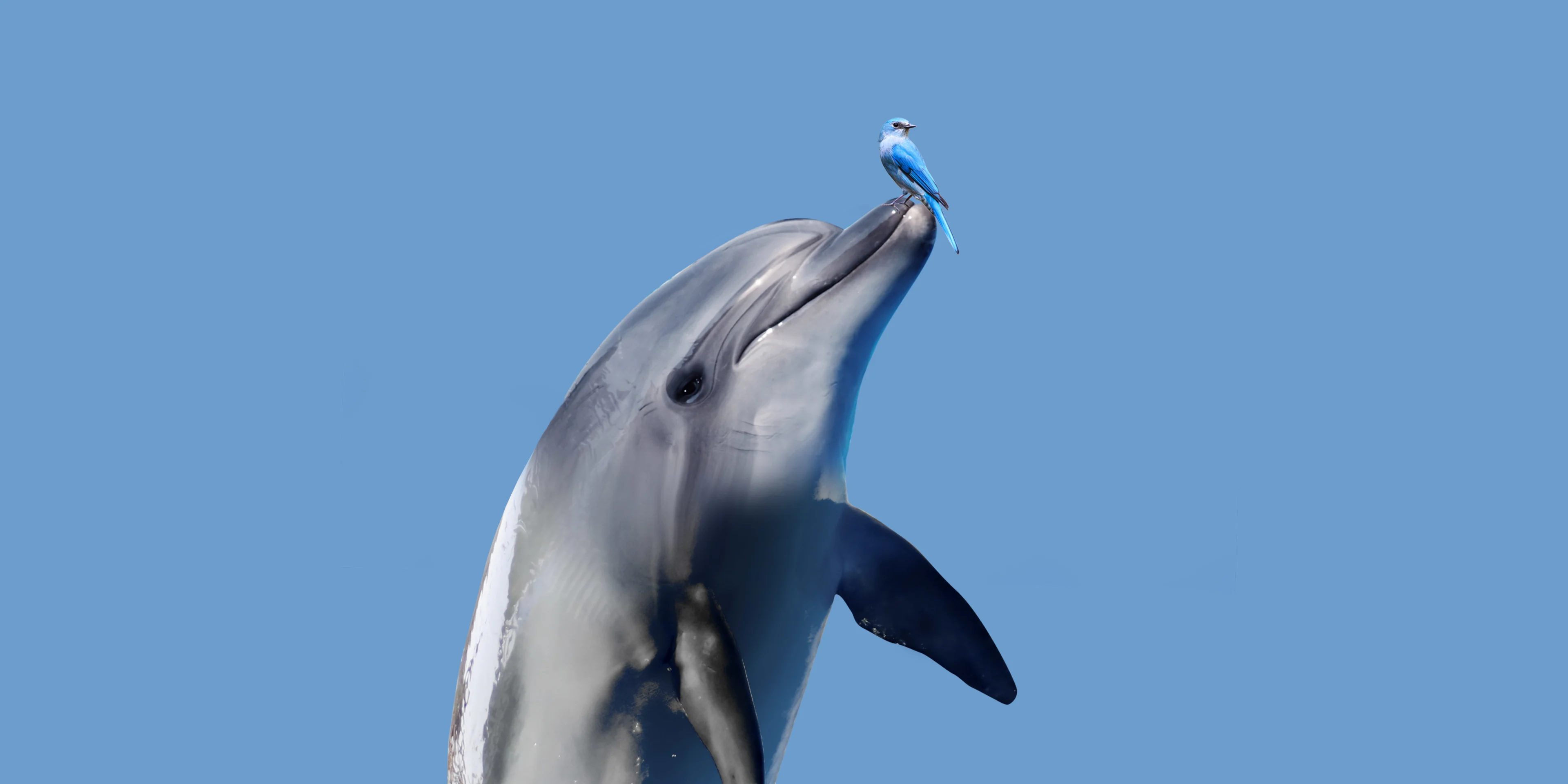
Circular economy
5 minute read
How unusual partnerships are fueling the circular economy
The challenges of sustainability are so huge that there is a limit to what one company can do on its own. Collaborations across value chains and even with completely different sectors are helping to unlock benefits that organizations cannot realize individually, leading the way to the circular economy holy grail.
In this article, we zoom in on innovative partnerships fueling the circular economy across industries. Find out how partnerships between different businesses are paving the way for car headlamps made from recycled plastics, zero emissions beer and shoe soles made from old car and truck tires.
Collaboration for sustainable plastics
Plastic pollution and the amount of fossil resources used in the materials' production are a case in point where innovative collaboration is key to making huge strides towards sustainability targets and helping companies in this sector transform to lower emission models.
A partnership between polymers company Covestro and Neste, a forerunner in renewable and circular solutions, shines the light on how a collaborative approach paves the way for a win-win approach.
“We have incredible possibilities to help tackle climate change by helping these industries.“
The strategic cooperation, announced in May 2020, aims to “promote the use of sustainable raw materials in plastics production.” The collaboration will see Covestro using material from renewable sources to replace a significant portion of the fossil raw materials that is currently being used to eventually make polycarbonates, high-performance plastics that are used in products such as car headlamps, LED lights, electronic and medical devices and automotive glazing.
“We have incredible possibilities to help tackle climate change by helping these industries,” says Jeroen Verhoeven, Vice President Value Chain Development in Neste’s Renewable Polymers and Chemicals unit.
“In chemicals, you can’t decarbonize like you can in other sectors. In transportation for example, we see the move towards electric mobility. But in chemicals, you need the carbon to make the products,” Verhoeven says.
“That means we have to make the best use of the carbon that is currently in circulation and circulate it again and again. At Neste, we take renewable and recycled raw materials and convert them into hydrocarbons that the petrochemical industry can use to make more sustainable plastics and chemicals.”
Neste produces its renewable hydrocarbons entirely from renewable raw materials, such as waste and residue oils, and fats. The recycled component is based on processing liquefied waste plastic.
“One of the benefits of these renewable hydrocarbons is that chemically, they are identical to the fossil products they replace“
In the short term, Neste will support Covestro in replacing several thousand tons of fossil raw materials with renewable hydrocarbons that are used to make polycarbonates. One of the benefits of these renewable hydrocarbons is that chemically, they are identical to the fossil products they replace in polymers production, so they are “drop-in” replacements.
“It means that converters, brand owners and OEMs (original equipment manufacturers) can use their existing infrastructure and existing assets. They don’t have to do any requalification of products,” Verhoeven says.
Involving the whole value chain
The partnership would be a lot simpler if Covestro was a direct customer of Neste, but that is not the case. In an illustration of how complex the chemicals supply chain can be, Neste supplies renewable feedstocks to companies such as Borealis, LyondellBasell, Mitsui or LG Chem, which then process them to provide companies such as Covestro with the materials they need to make a range of plastics and other products.
“It would be easier if we were a direct supplier,” says Verhoeven. “Instead, we are working with companies downstream, which makes it more unusual. We don’t just treat Covestro like partners – we also have to build partnerships with the company’s suppliers. The entire value chain needs to be involved.
“We are not a plastics producer and we have no plans to become one,” he adds. “So, we can’t do this on our own.”
Odd couples walking the circular economy talk
As circular economy principles gain further traction, such unusual partnerships are becoming more common. Heineken’s zero emission Gösser brewery in Austria obtains about 40% of its heat requirements using waste heat from a sawmill situated a few hundred metres away. It then borrowed the idea for its brewery in Meoqui, Mexico, which uses waste heat from the glass factory next door in its beer-making process.
Timberland, the apparel maker famous in particular for its boots, has created another unlikely partnership. Looking for opportunities to increase the amount of recycled materials in its products, in 2008 it started using recycled soles made with rubber from discarded truck and car tires.
However, as demand for its products increased, it could no longer guarantee the quality of the recycled rubber. So, in 2010, it developed a product with at least 35% recycled latex, reusing pre-consumer rubber that would have otherwise gone into landfills.
“But the most sustainable recycled content is made with post-consumer recycled materials so we asked ourselves: ‘Is it possible to introduce a car tire that is designed and manufactured with a designated second life as an outsole in Timberland shoes and boots in mind?” the company says.
It then joined forces with tire maker Omni United to create a range of premium car tires that could be recycled into Timberland boots or shoes once they reached the end of their life on the road. The Timberland branded tires are the first ever designed to be repurposed at end of life.
Meanwhile, German tire maker Continental is using reprocessed polyester from recycled PET plastic bottles in its products, with a full set of tires using more than 60 bottles.
“This is all circular economy in action and we see a lot of acceleration in that direction.“
In the future, recycled plastic will become an increasingly important raw material also for companies like Neste. “The raw material pool we use will grow and evolve in the future,” Verhoeven says.
“Heineken, with its energy recycling, and Timberland’s use of mechanical recycling are great examples of how to build old materials into new forms.”
He adds: “This is all circular economy in action, and we see a lot of acceleration in that direction. Previously, by many in the chemicals world, the circular economy and sustainability were seen as a threat. But companies now realize it is an opportunity, if we do it right. Collaborating on bringing sustainable products to market is also a lot of fun.”
Credits: Mike Scott, An award-winning business and environmental journalist whose work has appeared in publications including the Financial Times, the Guardian and Forbes.