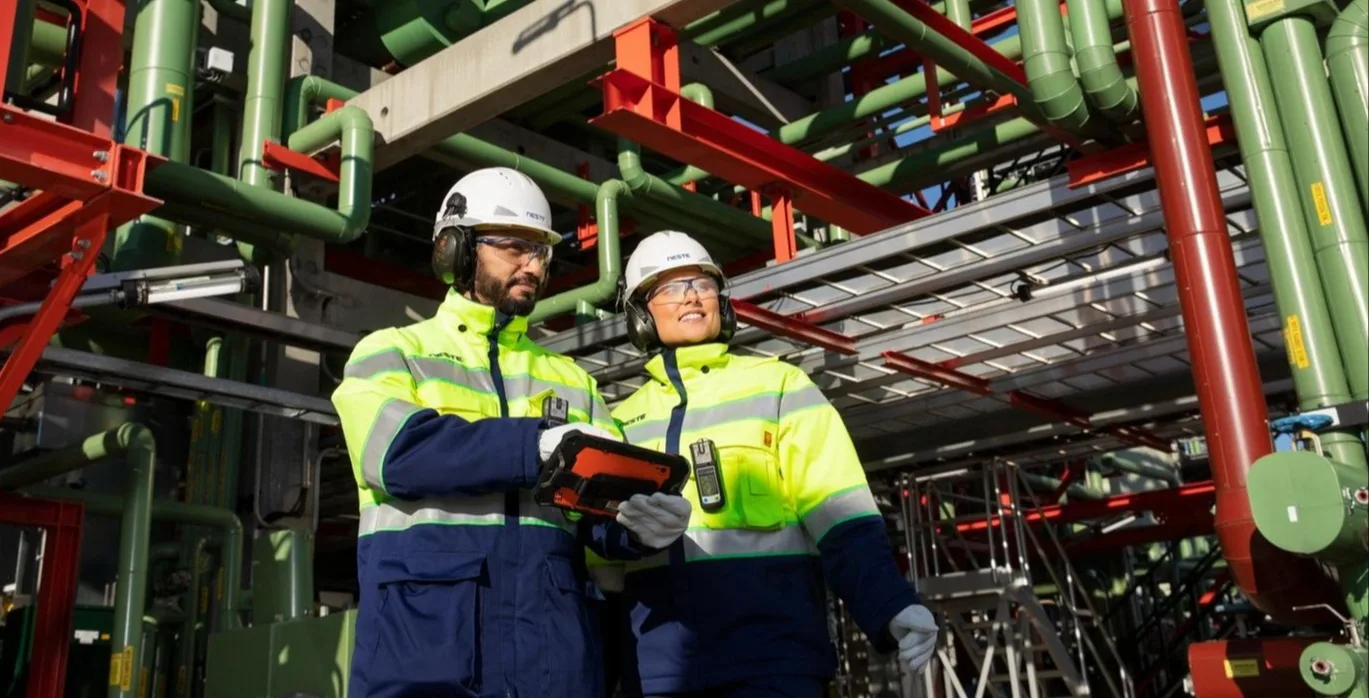
Our offering
Connecting research and innovation to technology development and engineering competence.
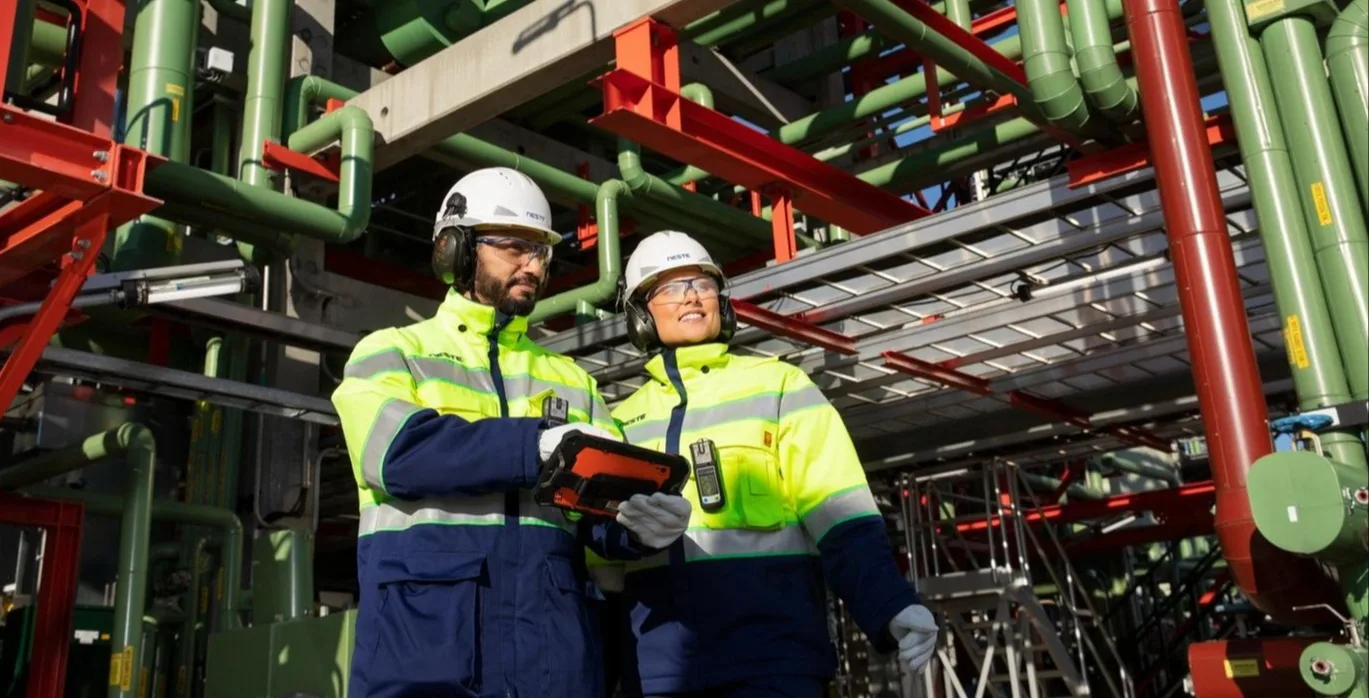
Finding new
Developing New Business Opportunities and Solutions
Building new
Planning and Implementing Investments
Improving existing
Continous Improvement & Operational Excellences
Growth and transformation by finding new, building new and improving existing for you
We find and develop new business opportunities with our customers by excellent use of our consulting and advisory services.
We connect research and innovation to our technology development and engineering competence and turn it into customer value.
We build new by planning and implementing investment projects and improve existing facilities with our portfolio of licensed process technologies, engineering capabilities and digital solutions. We facilitate our customers' transformation towards production investments and operations that meet future technology and sustainability demands.
Seamless collaboration with an experienced and innovative technology-focused partner
In addition to providing licensing and typical pre-engineering through basic engineering and detailed engineering up to EPCM (Engineering Procurement and Construction Management) and start-up of chemical plants (engineering services), we enjoy working in close collaboration with companies’ R&D organizations and start-ups at an early stage of design. This often includes rough cost estimation and concept engineering.
We often have helped to speed up development and upscaling via simulation and deep chemical process know-how, originating from our vast refinery heritage. Also this type of development needs to be taken into account when assessing the full investment cost of a plant to be running a new or revamped process with an unknown concept.
Recently we have developed the following project types:
technical due diligence
techno-economic analysis
technology benchmarking
technology verification
process concept development
licensor’s process design packages (PDP)
debottlenecking and equipment renewals
owner’s engineering
basic engineering
upgrading studies
safety improvements
EPCM deliveries
automation deliveries
energy integration
CAPEX/OPEX estimation
licensors services
Read more about our offering:
Feedstock Processing
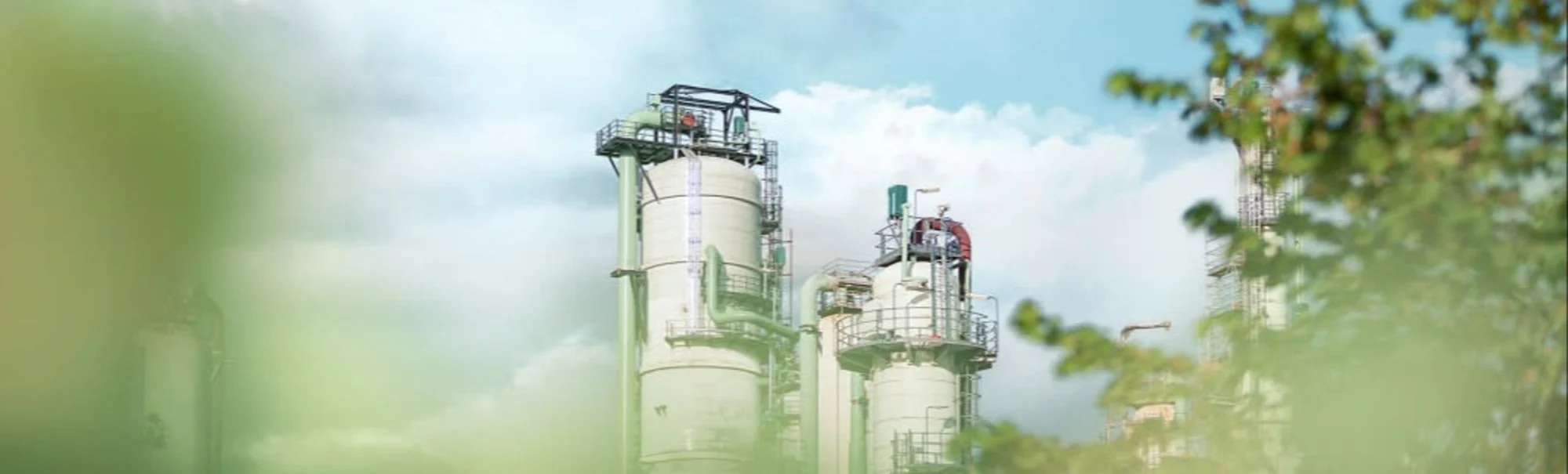
Expertise in more complex feedstocks
Our vision is to help our customers to convert various bio-based feedstocks, side streams or wastes into more valuable chemical intermediates or final products through our extensive understanding of pre-treatment of various feedstocks to meet the purities needed for example in catalytic processes and finally converting the intermediates into high quality products.
One of the main challenges is the ability to convert more complex bio-based feedstocks in most cost effective ways or use it in novel industrial applications. We provide world class solutions to this challenge, for instance, our projects have included conversion of lignocellulosic feed into ethanol and further to higher alcohols such as butanol, pyrolysis and gasification processes.
Our customers in this industry range from small start-up companies to large scale renewable diesel, renewable jet, oleochemical such as tall oil and pulping industry companies. Typical product application is often based on lignocellulosic feedstock, vegetable oils or animal fats.
Global leader in Crude Tall Oil fractionation
We have accumulated vast experience in Crude Tall Oil (CTO) fractionation over the last 40 years in the Feedstock Processing industry. We are the global leading company focused on CTO fractionation process licensing, engineering and optimization.
Neste’s proprietary NEXPINUS™ technology is licensed globally today. In the value and production chain, such CTO fractionation comes after soap extraction and Crude Sulphate Soap (CSS) acidulation. Typical scale of a single CTO fractionation unit is from 50 to 200 ktons CTO feedstock per annum.
The recent global interest in new bio-based feedstocks has also increased interest in Crude Sulphate Soap and Tall Oil fractionation processes, resulting in several new patents in the field. We have the newest industry insights, an end-to-end process concept, reliable and unbiased estimates and a solid partner network. Our technology enables optimal and flexible design based on a proprietary model with the possibility to evaluate future feedstocks.
No need for a pilot plant
The feedstock processes we co-developed, developed or verified are based on process modeling and simulation. For that purpose, we have a substantial range of in-house vapour-liquid data banks and programs for fitting the kinetics and equilibria. Modeling provides detailed understanding of the process and mitigation of risks at an early stage of the investment cycle.
Our systematic approach for process development ensures efficient progress towards commercialization of new technologies. This means that our customers will enjoy earlier entry to the markets with new processes developed as in most cases large-scale and costly piloting is not needed.
An additional benefit of simulation is that the process can be tailored for a wide range of feedstocks. A well known industry landmark project based on this type of simulation based technology commercialization and skipping the pilot is Neste’s NEXBTLTM technology. The capacity of the first NEXBTLTM unit was already 170 000 tpa.
Refining and Petrochemicals
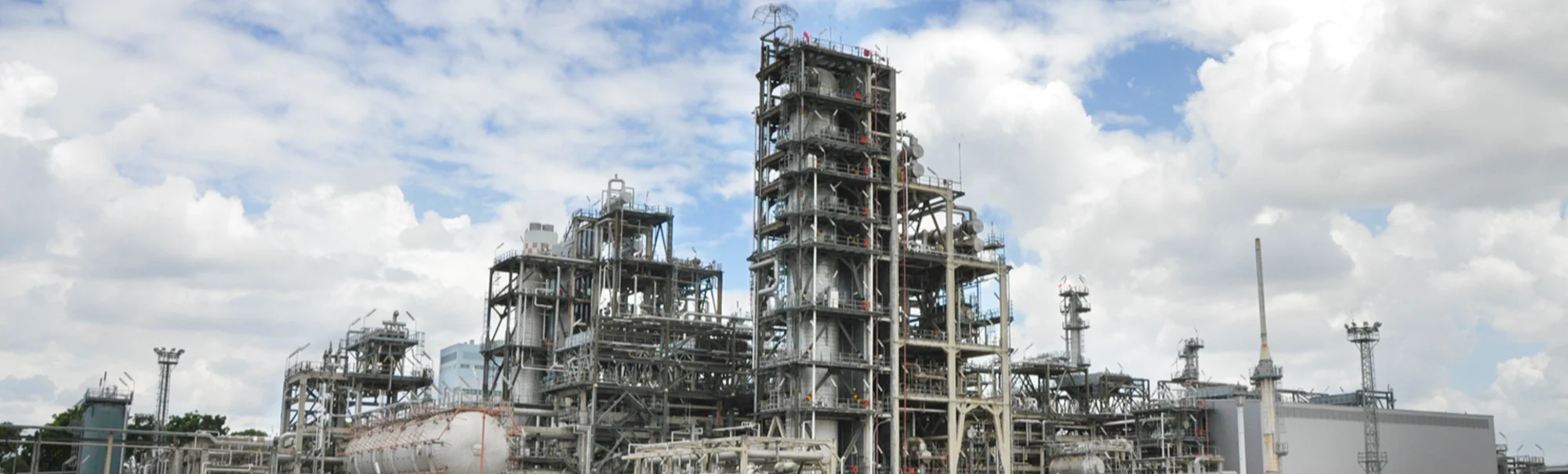
Strong process and technology know-how
Over 60 years in the Oil Refining industry has given us extensive knowledge and high expertise in various fields. We also have a successful track record in the Petrochemicals industry from the past 50 years.
Our strengths are in demanding front-end studies, distillation technology, energy optimization, refinery integration, and complex turnarounds. We have the ability to deliver challenging projects safely, cost-effectively, meet high quality standards and significantly improve the performance of our customers’ existing or future plants.
Service portfolio
We have an extensive understanding of refining sour crude oil to various high quality products. For instance, in our projects we have solved several challenges with Solvent Deasphalting (SDA) and Sulfur Recovery Units (SRU) to make refineries operate more efficiently and sustainably.
Furthermore, we are experts in optimizing and integrating our customers’ site infrastructure for example in energy, utilities and chemical storing and transportation to meet the demands of their production.
Renewable Gas and Chemicals
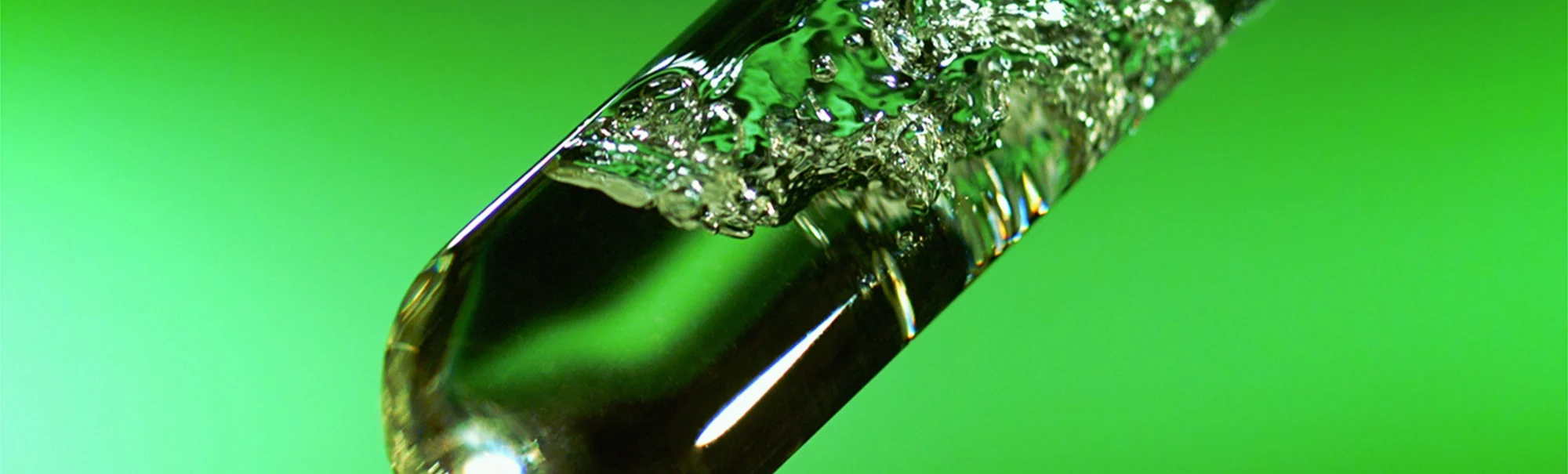
Reduce carbon emissions and increase renewable carbon content
In the Renewable Chemicals and Gas (RCG) area our vision is to reduce Your carbon emissions and increase Your renewable carbon content and material recycling rate through flexible process design, licensing or developing and upscaling new processes and technologies together.
We provide the RCG industry with technology and engineering solutions that help replace virgin fossil feedstock in the production of chemicals and gases, including transmission of gases of various nature (from LNG to synthetic and renewable gases). Our current customer base in this industry segment covers, among others, brand owners, chemical companies, pulp and paper companies and start-up companies.
First-of-a-kind processes to serve renewable industry
At Technology and Engineering, we have a unique track record in designing first-of-a-kind processes and plants in the renewables space – spanning over all industry segments we serve – including, woody biomass gasification (Biomass-to-liquid, “BtL”), carbon capture and utilization (CCU,) Power-to-X (P2X, PtX, PtL), renewable gas transmission and xylose sugar separation, among others.
Today, our vast know-how of bio-based and thermochemical unit processes can be combined with our hydrocarbon industry process know-how to develop new solutions for sustainable chemicals and gases from e.g. lignocellulosics, recycled plastics or renewable gases.
Hydrocarbon know-how is represented by a deep understanding of hydrogen processes, such as hydrogenation and hydrocracking. Through our biomass-to-liquid work, we are familiar with the Fischer-Tropsch (FT) synthesis. Many processes need purification, separation and fractionation expertise, which we can handle through vacuum distillation expertise.
In addition to our ability to develop and implement first-of-a-kind processes, we have the ability to integrate these often novel unit processes into a complete end-to-end process with the necessary utilities and effluent treatment units. These critical and costly functions are oftentimes overseen in new technology development projects emphasizing the need for a competent multi-industry and technology-oriented process integrator and coordinator, possibly acting as a licensor.
Life Science
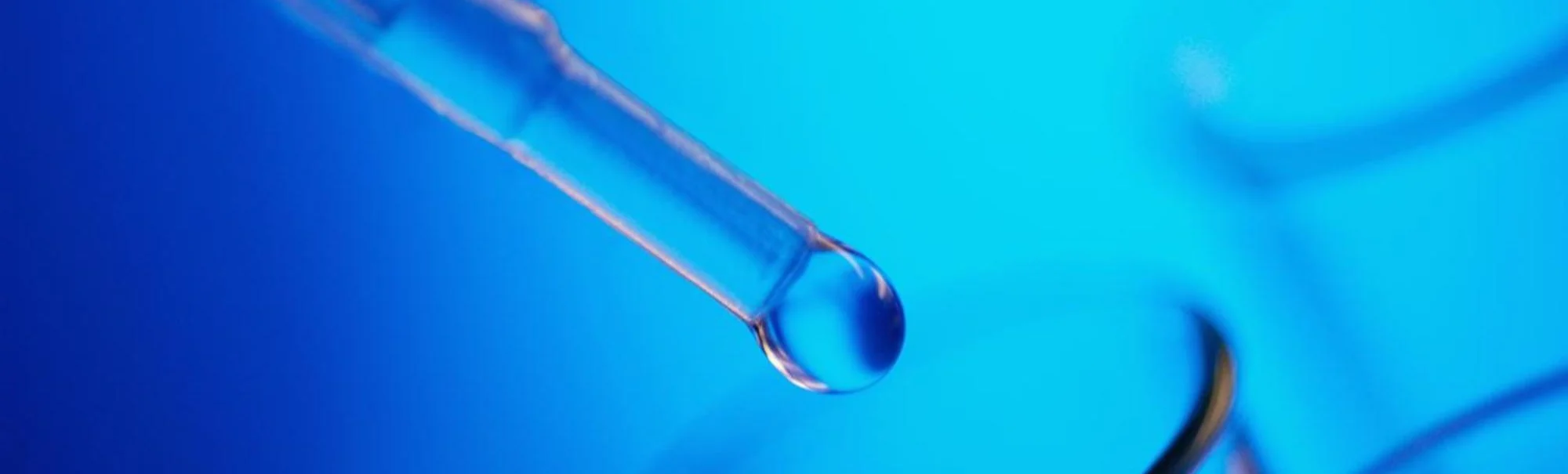
Understanding of the complex processes
Biopharma, food and feed plants rely on a high level of expertise to design complex processes that produce edible oils, natural sweeteners (e.g. xylose and xylitol, sucrose, glucose, fructose and sugar syrups), beverages active food ingredients (e.g. esters and sterols), industrial enzymes for feed applications and other products in demand. They must comply with strict cGMP requirements for hygienic production and cleanliness, and simultaneously be flexible enough to utilize various feedstocks and valorize all side streams for the best possible plant profitability.
Through these projects, we have perfected working and designing according to the GMP (Good Manufacturing Practices) and various levels of hygienic production. Methods and unit processes used in plasma fractionation, where protein fractionation is in the core, can also be modified and applied to other novel industries, such as new meat alternative protein development and process upscaling, or for algae separation processes.
Experts in human blood plasma fractionation
For 40 years, we have been experts in human blood plasma fractionation, one of the most complicated and regulated pharmaceutical sectors. Our in-depth understanding of the industry, its life-saving products and tough regulations mean that we can truly build quality into our designs for plasma and biopharmaceutical production. We carefully mitigate the risk factors, and design processes that are easy to validate, ensuring the repeatability and traceability of your final product.
We provide you with end-to-end solutions, from business planning, technology selection and concept design to delivery and beyond. Our understanding of plasma process technologies, production processes, operational aspects, automation and cost levels, help us to design and integrate innovative and highly advanced, yet robust and economical solutions into your plant.
By combining our interdisciplinary bioengineering skills, international experience and a library of specialized solutions, we can design your facility to produce a full range of plasma-derived medicinal products (PDMPs) or other biopharmaceuticals. Our collaboration with big industry players extends our global reach, but we are small enough to give you personal service. There is an urgent need for PDMPs worldwide, especially in developing economies. We are dedicated to creating safe and cost-effective solutions to help patients everywhere.
Innovative end-to-end engineering services for the food and feed industries
For decades, we have been planning facilities for food industry companies and animal feed manufacturers. Such plants rely on a high level of expertise to design complex processes that produce edible oils, natural sweeteners (e.g. xylose and xylitol, sucrose, glucose, fructose and sugar syrups), beverages active food ingredients (e.g. esters and sterols), industrial enzymes for feed applications and other products in demand. They must comply with the strict GMP requirements for hygienic production and cleanliness, and simultaneously be flexible enough to utilize various feedstocks and valorize all side streams for best possible plant profitability.
We maximize the production capacity and energy efficiency of your plant. Our design is based on the process solution combined with sophisticated automation solutions and layout. Depending on the key selection criteria, such as maturity of the process, availability of equipment, location and schedule, the dimensioning of the key equipment can be based either on integration of equipment skids or individual equipment. In addition to our extensive process simulation and modeling capabilities, our process optimization technology NAPCON is a valuable tool in the complex task of factory integration.
By combining our unique multidisciplinary knowledge, including a comprehensive understanding of biopharma and biorefining, we can provide you with innovative end-to-end engineering services for the food and feed industries. We thoroughly understand industry processes, so your new or existing plant will have quality designed into it.
Our track record showcases our skills in core process development, aseptic design and competence in several unit operations including fermentation, precision fermentation, crystallization, evaporation, extraction, filtration, centrifugation, deodorization, stripping, pastillation, bleaching and many others. Our protein design project family also includes Single Cell Protein (SCP) from lignocellulosics biomass side streams as well as alternative plant-based proteins.