Optimum Hydrogenation Technologies for Fuels and Solvents
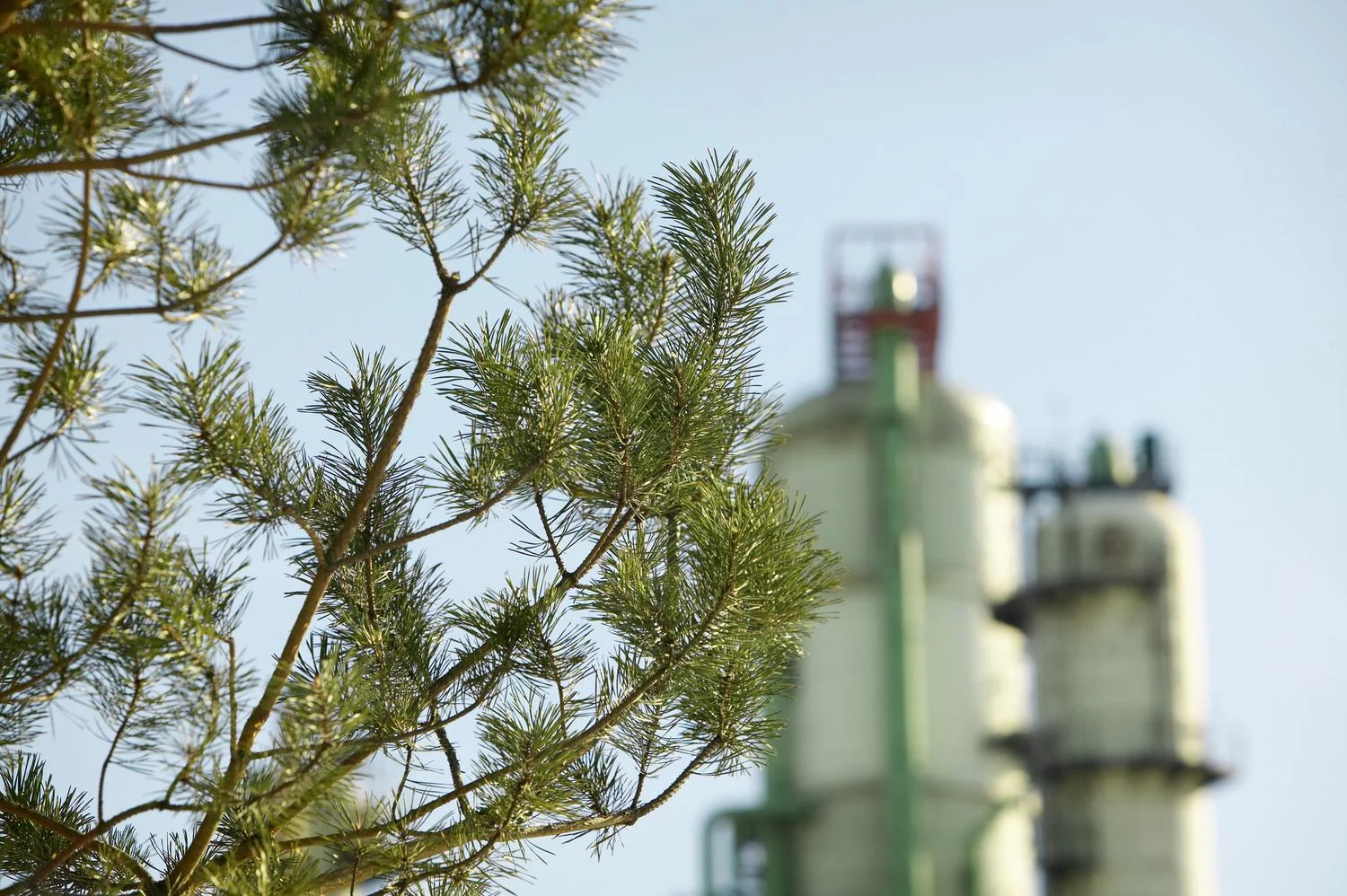
NEXSAT is the optimum technology for aromatics reduction and olefin saturation
Fuel and solvent manufacturers can now meet current and future olefin and aromatic strict saturation standards safely and economically with a high availability process at low cost.
Neste's NEXSAT is the optimum process for hydroprocessing of low-sulfur feedstock in mild operating conditions, followed by product property fine-tuning in a stabilization or fractionation section for the ultimate quality gain.
Typical products are low aromatic fuels, aromatic free solvents, and highly saturated fine hydrocarbon chemicals.
Our flexible NEXSAT process can be used for saturation of a wide range of olefinic feedstocks or dearomatization of middle distillates and naphtha, in a design optimized for single or multiple feedstocks. Capital outlay is kept to a minimum, often with no need for a dedicated fired heater nor recycle compressor, while retaining excellent operational availability and low maintenance requirements. Add to that the low cost of catalyst, excellent reactor performance and its high-quality output, and you are sure to find it a wise investment.
Numerous benefits of NEXSAT technology
Economical Benefits
• Highly effective dearomatization catalyst at low cost
• Low investment and operating costs
Flexibility and easy operability
• Flexible and advanced aromatic and olefin hydrogenation technology
• Excellent reactor performance at mild operating conditions
Typical Product Qualities
• Naphtha max. 0.1 vol-% benzene
• Middle distillates max. 5 vol-% aromatics
• Solvents max 0.5 vol-% aromatics
• Light hydrocarbons olefin saturation max 200 vol-ppm Olefins
NEXSAT brochure
Download our essential product information on NEXSAT technology
NEXSELECT for selective diolefin hydrogenation
Reliable processing with high availability is of greatest importance for producers of petrochemicals. Light cracked naphtha always contains diolefins that form gums and cause equipment fouling and product degradation among others in etherification units. Neste's NEXSELECT process removes this problem by selective hydrogenation.
Mild temperature eliminates the formation of paraffins, improving the overall yield in these downstream units. The result is a clean and trouble-free flow throughout your process and better quality in your final product.
Investment is minimal because NEXSELECT operates in liquid phase and does not need a hydrogen recycle compressor. It is easily integrated into NEXTAME and NEXETHER units without more degasification equipment. Low cost for high return is always a wise business choice.
Numerous benefits of NEXSELECT technology
High conversion of Diolefins
• Trouble-free operation without any gum formation in e.g. etherification reactors downstream
• Improves naphtha value as blending component
Low Investment Cost
• Operates at liquids phase and does not need any hydrogen recycle compressors or gas separation if integrated into downstream distillation units
Proven Design and high availability
• Optimum performance and high availability
• Track record with proven design and easy operation
NEXSELECT brochure
Download our essential product information on NEXSELECT technology
Download now (pdf)
Share this